3Dプリンターとは?
2021.03.01 更新日:2024.02.28
- 3Dプリンター
製造業をはじめとする物づくりの現場で注目されている3Dプリンター。自社での導入を検討されている方も、多いのではないでしょうか。
この記事では、初めての3Dプリンター導入を検討されている方へ向けて、3Dプリンターの基礎知識をわかりやすくご紹介していきます。
3Dプリンターとは?
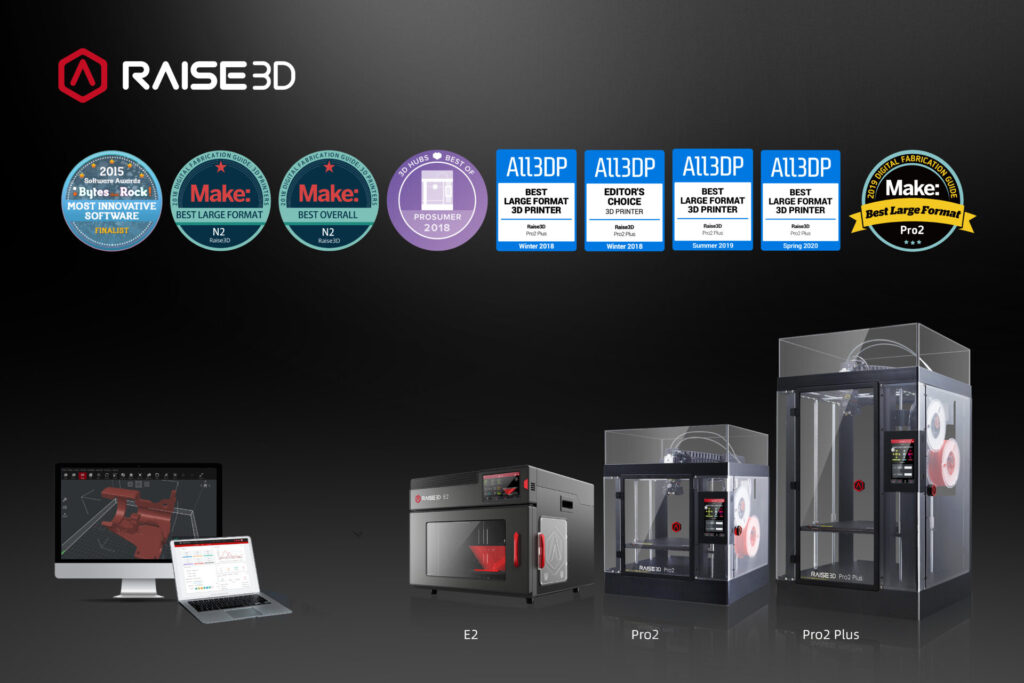
3Dプリンターとは、立体物を造形できるプリンターのことです。3DCADなどの三次元データをもとに、金型を使わず、材料を積層することで立体物を造形していきます。
造形方式は1つではなく、熱で溶かした樹脂を積み重ねていったり、液体樹脂を紫外線で硬化させたり、粉末材料に接着剤(バインダー)を吹き付けて固めたりとさまざま。
また材料も、プラスチックを中心に、ゴムや石膏、金属まで、さまざまなものを使用して造形することができます。
3Dプリンターの使用用途
3Dプリンターは、物づくりにおけるさまざまなシーンで活用することができます。
サンプル・模型の製作
3Dプリンターで商品のサンプルや模型を製作すると、完成イメージをより具体的に共有することができます。
商品企画のプレゼンや営業活動の際にサンプルや模型があれば、仕様書やデザインイメージだけを提示して説明するよりも、訴求力がアップすることは間違いありません。
試作品の製作
通常試作品は、製品設計や開発の最終段階、大量生産の前に製作しますが、3Dプリンターがあれば、初期段階から試作品を製作し、内部構造や動作を確かめながら開発を進めることができます。
外部に依頼するよりも短納期で試作品が仕上がるため、製品開発の期間を短縮可能。また何度改良版の試作品を製作しても、それほどコストは嵩みません。従来よりも、短期間・低コストで、より品質の高い製品を生み出すことができます。
型・治工具の製作
3Dプリンターでは、製造や組み立ての現場で使用する型や治工具も造形できます。製品設計や開発では、改良を加えながら何度も金型を製作する必要がありますが、3Dプリンターであれば、短期間・低コストでの改良が可能です。
また型や治工具が破損した場合や、追加で必要になった場合にすぐに造形できるのはもちろん、仕様変更が発生した場合でも、3Dデータを編集すればすぐに新しいものを造形できるため、生産性がアップします。
最終製品の製造
もちろん、3Dプリンターで最終製品を製造することも可能です。特に特注品や数量限定品、急ぎ納品が必要なパーツなどの製造に向いています。
また3Dデータさえあれば、いつでも何度でも同じものを造形できるため、修理や交換用部品の在庫を抱える必要が無くなり、さらに、既に製造終了したパーツをスキャンして3Dデータを作成すれば、再び同じパーツを造形することも可能です。
医療用パーツの製造
3Dプリンターを使えば、人工骨やインプラント、義手など、複雑な形状で精密さが求められる医療用パーツも造形することができます。
医療用パーツは、量産ではなく、患者一人ひとりに合ったオーダーメイドが求められる場合も多いですが、3Dプリンターであれば、比較的短納期・低コストで造形することが可能です。
また3Dデータを編集するだけで改良できるため、患者の成長に合わせてパーツを作り替えていくといったことも、簡単にできます。
3Dプリンターでの造形工程
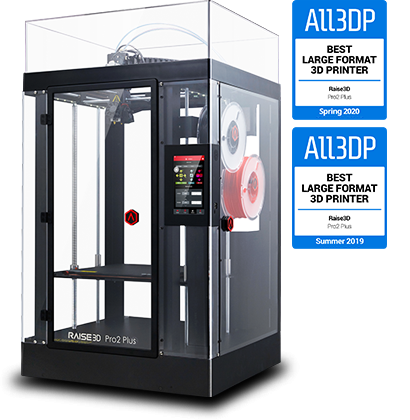
3Dプリンターで造形物を製作する流れを、簡単にご紹介します。
1.3Dデータの作成
3Dプリンターで造形するには、3Dデータが必要です。まずは、3DCADなどのソフトウェアを使って、3Dデータを作成します。既に存在しているものをスキャンして3Dデータを作成したり、配布サイトからダウンロードしたりすることも可能です。
3DCADデータが用意できたら、3Dプリンターに対応している「STL形式(.stl)」か「OBJ形式(.obj)」に変換し、データにエラーがないかチェック。
データに問題がなければ、スライスソフトで造形時のさまざまな設定を行い、3Dプリンターのヘッドの動作を制御する「造形パスデータ」へと変換します。
3Dデータの作成方法についての詳細は、「3Dプリンター用データの作成方法は? データ作成後の手順やデータ作成時の注意点まで徹底解説」のコラムをチェックしてみてください。
※関連コラム:3Dプリンター用データの作成方法は?データ作成後の手順やデータ作成時の注意点まで徹底解説
2.3Dプリンターで造形
「造形パスデータ」を、3Dプリンターに送り、必要な材料をセット。あとは各3Dプリンターの手順に従って造形を開始すればOKです。
3.造形物の後処理
3Dプリンターで製作した造形物は、基本的に後処理が必要です。後処理の工程は、乾燥や冷却、洗浄、研磨など、造形方法や素材、求める完成品の状態などによって異なります。
またサポート材を使用した場合は、それらの除去が、金属3Dプリンターの場合は、造形方法によっては脱脂や焼結が必要です。
3Dプリンターの主な造形方式
一口に3Dプリンターと言ってもさまざまな造形方式があり、使える素材やメリット・デメリット、向いている用途などがそれぞれ異なります。
ここでは、一般的な3Dプリンターの造形方式である「熱溶解積層方式(FDM方式)」「光造形方式(SLA方式/DLP方式)」「粉末焼結方式(SLS方式)」「インクジェット方式(材料噴射方式)」「バインダージェット方式」の5つについて、わかりやすくご紹介していきます。
熱溶解積層方式(FDM方式)
現在3Dプリンターの造形方式で主流となっているのが、熱溶解積層方式です。個人向けの3Dプリンターも、ほとんどがこのFDM方式。
フィラメントと呼ばれる熱可塑性樹脂を溶かしてノズルから押し出し、一筆書きで1層ずつ積層し、造形していきます。
熱溶解積層方式のメリットは、比較的造形物の強度が高いこと。またフィラメントは細い紐状で扱いやすく、溶かした樹脂はすぐに冷えて固まるため、液体樹脂や粉末材料よりも比較的手軽で安全に造形できます。
さらに、主流な造形方式であることから、さまざまなフィラメントが登場していて、材料の選択肢が豊富なのも嬉しいポイント。
デメリットは、積層部分の凹凸が目立ちやすく、滑らかさが求められる造形には不向きなことです。
サンプル・模型や試作品、型・治工具の製作のほか、強度重視の最終製品の造形にも向いています。
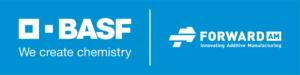
光造形方式(SLA方式/DLP方式)
光造形方式は、3Dプリンターの造形方式の中で最初に開発された方式です。
ステージと呼ばれる造形台が降下し、紫外線で固まる液体樹脂で満たしたプールに浸かります。
プールの下から、ステージに向かって紫外線を照射し、一層分を硬化。一層でき上がったらステージが上昇し、余分な液体樹脂を落としてから、再び降下します。
前回よりも一層分高い位置でステージが停止し、再び紫外線を照射して硬化。これを繰り返して造形していきます。
SLA方式とDLP方式の違いは、一度に照射できる面積です。
SLA方式は、点で照射していくため、造形スピードは遅いですが、造形精度は高いです。
一方DLP方式は、面で照射していくため、造形スピードは速いですが、造形精度はSLA方式に比べるとやや劣ります。
光造形方式のメリットは、熱などによる変形が少ないため、精度が高く、滑らかな造形物を製作できること。また透明度の高い造形物も作ることができます。
デメリットは、紫外線で硬化するため、太陽光などが当たるところで使用すると、劣化するおそれがあること。
またアルコール溶剤を使用した洗浄などの後処理が必要で、造形にやや手間がかかるといった点も。
強度や耐久性よりも、見た目の美しさを重視するフィギュアなどの最終製品の製造に向いています。
粉末焼結方式(SLS方式)
粉末焼結方式(SLS方式)は、光造形方式(SLA方式/DLP方式)の材料が粉末材料になり、紫外線がレーザー光線になったものと考えて差し支えないでしょう。
ステージに粉末材料を敷き詰め、そこにレーザー光線を照射して焼結。一層でき上がったらステージが下がり、造形物の上にまた粉末材料を敷き詰め、再びレーザー光線を照射して焼結。これを繰り返して造形していきます。
粉末焼結方式(SLS方式)のメリットは、耐久性に優れた造形物ができ上がること。また敷き詰めた粉末材料が支えになるため、サポート材が不要です。材料に金属粉末を使用できるのも、メリットの一つとして挙げられます。
デメリットは、造形物の表面に、粉末のざらざらした質感が残ってしまうこと。また健康被害や事故を防ぐための、粉じん対策が必要になります。
試作品のほか、耐久性に優れているため、表面の質感が問題なければ、最終製品の造形にも向いています。
インクジェット方式(材料噴射方式)
インクジェット方式(材料噴射方式)は、紫外線で固まる液体樹脂をインクヘッドから噴射、紫外線を照射して硬化を一層ずつ繰り返していく造形方法です。
インクジェット方式(材料噴射方式)のメリットは、樹脂の噴射量をコントロールできるため、高精細で滑らかな造形物ができ上がること。
また造形スピードが速く、フルカラーでの着色や複数材料を混合利用することも可能なので、着色やアッセンブリといった工程も短縮することができます。
紫外線で固まる液体樹脂を使用する点は、光造形方式(SLA方式/DLP方式)と同じですが、液体樹脂を満たしたプールが必要ないため、安全性や設置の容易さという点ではインクジェット方式が上回ります。
デメリットは、耐久性が低く壊れやすいこと。また光造形方式(SLA方式/DLP方式)と同じく、太陽光などが当たるところで使用すると、劣化するおそれがあります。
ゴムなどの材料を使用した試作品の製作や、フィギュアなどの最終製品の造形に向いています。
バインダージェット方式
インクジェット方式と同じく、インクヘッドから噴射する方式ですが、バインダージェット方式では、敷き詰めた粉末材料に接着剤(バインダー)を噴射し、造形していきます。
バインダージェット方式のメリットは、粉末であればどんな材料でも使用できること。石膏や金属のほか、食品を造形できる3Dプリンターも開発が進められているそう。
また造形スピードが速く、敷き詰めた粉末材料が支えになるため、サポート材が不要です。
デメリットは、強度が弱く、表面に粉末のざらざらした質感が残ってしまうこと。また粉末除去などの後処理や、健康被害や事故を防ぐための粉じん対策といった手間もかかります。
強度や耐久性を求めないサンプル・模型の製作や、フィギュアなどの最終製品の造形に向いています。
3Dプリンター導入のメリット・ベネフィット
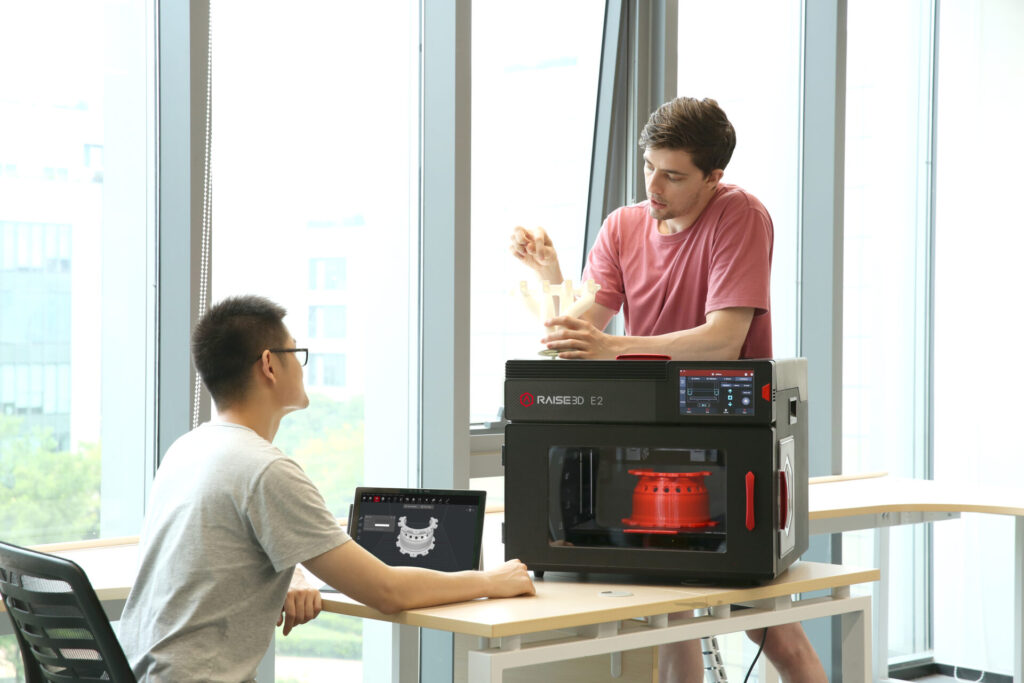
物づくりの現場で3Dプリンターを導入すると、さまざまなメリットやベネフィットを得ることができます。
1台あればさまざまな素材を使った、さまざまな造形物を製作できる
造形方式にもよりますが、1台の3Dプリンターで使用できる素材は1つではありません。プラスチックはもちろん、ゴムや金属など、さまざまな素材で造形できます。
また形状に対しての制約はほとんど無く、3Dデータさえあれば、従来の製造技術では難しかった形状の造形物も製作することが可能です。
3Dプリンターが1台あれば、比較的簡単に新しいアイディアを製品化することができます。
開発期間の短縮
3Dプリンターがあれば、3Dデータを用意するだけですぐに試作品を作成することができるため、外部に試作品製作を依頼するよりも、開発期間を短縮することが可能です。
社内で試作品を作る際に必要だった金型を用意する必要もなく、また金型自体も3Dプリンターで造形できるため、こういった部分でも開発期間を短縮できます。
コスト削減
3Dプリンターがあれば、さまざまなシーンでコスト削減が可能です。
基本的に、3Dプリンターは必要な分量の素材のみを使用するため、無駄が出にくく、製品によっては、元の製造方法から3Dプリンターに切り替えるだけで、材料コストを削減できる場合もあります。
また開発段階で、試作品製作を外部へ依頼するコストを削減できるのはもちろん、それほどコストをかけずに何個も試作品を製作することができるため、試作品に改良を加えながら何度も検証を重ねることができ、最終段階からの手戻りによる金型作り直しといった無駄なコストや、それによる発売延期などの機会損失も減らすことができます。
さらに、最終製品の製造段階でもコスト削減が可能です。
複数のパーツをバラバラに製造して組み立てていたものを、組み立てた状態で造形することで、組み立てのための人件費や接合部分の材料費の削減、さらには製品の軽量化も実現できます。
在庫を抱えなくてよくなる
これまで、物づくりの現場や精密機器を使用する現場では、故障などに備えてパーツの在庫を抱えておくのが一般的でした。
しかし、3Dプリンターと3Dデータがあれば、いつでも簡単に必要なパーツを製造できるため、多量の在庫を抱えておく必要がなくなります。在庫を置いておくスペースや管理コストを削減できるほか、万が一、在庫に不具合が見つかった場合に、無駄になるといったことも起こりません。また各拠点に3Dプリンターを設置し、3Dデータを共有しておけば、パーツが必要な場所から最も近い拠点で製造、発送できるので、輸送費も削減できます。
少し改良を加えたいと思った時に、既存製品の在庫数を気にせず、3Dデータを変更して簡単に改良パーツを製造できるのも嬉しいポイントです。
活発な意見交換が行われる/認識の齟齬が起きにくくなる
3Dプリンターがあれば、サンプルや模型を用意して、企画・開発会議を行うことが可能です。目の前にサンプルや模型があれば、設計図やデザインイメージを見ながらよりも、もっと具体的なアイディアが生まれ、活発な意見交換が行われるようになります。
実物を目にしているので、認識の齟齬も起きにくく、より満足度の高い製品を完成させることができるでしょう。
作業効率/品質の向上
物づくりの現場では、パーツが足りないなどの理由で作業がストップしてしまうことがあります。しかし、3Dプリンターがあれば、必要な時に必要なパーツを造形して、すぐに作業を再開することが可能です。
また先ほどもお伝えしましたが、それほどコストをかけずに何個も試作品を製作することができるため、開発中に繰り返し検証や改良を重ねることができ、従来よりも短期間・低コストで、より品質の高い製品を生み出すことができます。
さらに、製品の設計変更などに合わせて、型や治工具調整なども簡単に行うことができ、細かい部分ですが、この点でも品質向上に繋がります。
3Dプリンターのデメリット
万能そうな3Dプリンターですが、いくつか向かない用途もあり、その点がデメリットとなります。
耐久性や強度が低くなりがち
造形方式や使用する素材にもよりますが、層を積み上げて造形するため、耐久性や強度が低くなりがちです。そのため、耐久性や強度が求められる最終製品の製造にはあまり向きません。
大量生産には不向き
3Dプリンターは、基本的に、素材コストが高く、また1つの造形にある程度時間がかかるため、大量生産には不向きです。そのため、受注生産やオーダーメイド、サンプル・模型、試作品の製作、現場で使う金型や治工具の製作など、比較的生産数の少ないシーンで導入するのがおすすめです。
初めての3Dプリンター導入なら、日本3Dプリンター株式会社へご相談ください!
一口に3Dプリンターと言っても、さまざまな製品があり、どんな目的でどのようなものを造形するかによって、最適な製品が異なります。初めての3Dプリンター導入でどの製品にするか迷っているのであれば、ぜひ、日本3Dプリンター株式会社へご相談ください。
日本3Dプリンター株式会社は、世界のトップメーカーの3Dプリンターを複数保有し、製品の特徴はもちろん、実際に使用して各造形方式の材料特徴(樹脂~金属)なども把握しており、3Dプリンターの選択や材料コンサルを含めたトータルのソリューション提案が可能です。
3Dプリンティングの専門知識を持ったスタッフが、貴社の課題を一緒に分析し、潜在的な問題を解決できる製品を導入するのはもちろん、メーカー認証資格を持つプロのエンジニアによる、ノウハウの共有やトラブル対応といった安心のサポートも提供しています。
お一人で悩まずに、ぜひ、お気軽にお問合せください。