3Dプリンターの造形の仕組みと知っておきたい基礎知識
2021.04.26 更新日:2024.08.23
- 3Dプリンター
3Dプリンターへの注目が高まっている現在、個人向けの安価なものから、法人向けの高価なものまで、さまざまな3Dプリンターが販売されています。
3Dプリンターには、主に7つの造形方式がありますが、3Dプリンターの購入をご検討中の方の中には、それぞれの造形プロセスや違いがよくわからないという方もいらっしゃるのではないでしょうか?
それはもしかしたら、3Dプリンターの基本の造形の仕組みをご存じないまま、それぞれの造形方式を理解しようとしているからかもしれません。
そこでこの記事では、3Dプリンターの造形の仕組みを始めとする、3Dプリンターを選んだり使ったりする上で知っておきたい基礎知識についてわかりやすく解説していきます。
3Dプリンターの仕組み
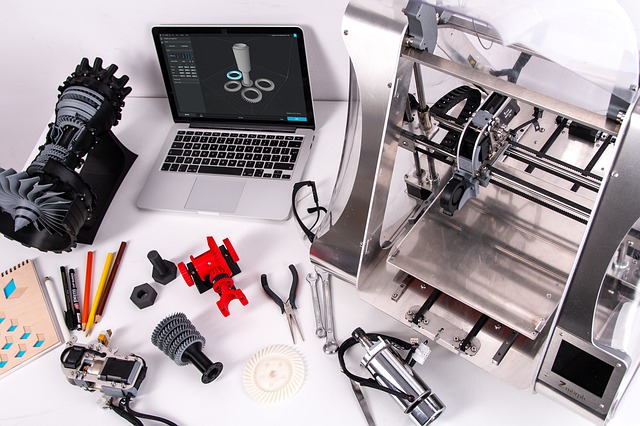
3Dプリンターの基本の造形の仕組みは、どの造形方式も同じです。
3Dデータを元に、何もない空間(ステージ)に材料を一層一層薄く積み重ねていくことで、造形物を作り上げていきます。
積み上げられていく層は、3Dデータを横にスライスした断面です。どこにどのように材料を積み重ねるかは、3Dデータによって制御されています。
では、造形方式によって、具体的にどんな部分が違うのかというと、使用する材料や材料の供給方法、結合方法に違いがあるのです。
3Dプリンターの基本の造形プロセス
ここからは、全ての造形方式の3Dプリンターに共通する、基本の造形プロセスをご紹介していきます。
3Dプリンターで造形をする場合は、造形の工程以外に、前工程と後工程が必要になります。
前工程
前工程で行うのは、主に3Dデータの用意です。
3Dデータは、3DCADソフトや3DCGツールで一から作成するほか、2DCADデータがある場合は、そのデータを3DCADデータに変換したり、3Dスキャナーを使って実物をスキャンしたりといった方法でも作ることができます。
また最近は3Dデータの無料配布をしているWebサイトなどもあるため、そこからダウンロードして利用することも可能です。ただし、ダウンロードした3Dデータは商用利用不可の場合もあるため、しっかりとWebサイトの利用規約を確認してから使用しましょう。
元となる3Dデータが用意できたら、3Dプリンターの専用ソフトウェアで読み込める形式で保存するか変換をします。
そして、3Dプリンターの専用ソフトウェア(スライスソフト)を使って、3Dプリンターを制御するための設定とスライスデータの作成を行います。
造形の向きは、造形物を横向きに設定するのが基本ですが、造形物の形状によっては、最も寸法差が出にくい向きを考えて設定する必要があります。
他に、積層ピッチや内部の密度、サポート部の有無もここで設定します。
サポート部は、必要に応じてソフトウェアが自動で設定してくれることも多いですが、造形の精度と後処理のバランスを考えて、元となる3Dデータを用意する段階で、作成者自身でサポート部の設定をしておいた方が良い場合もあります。
一通りの設定が終わったら、ようやく3Dデータの用意が完了です。
3Dデータの作成については、「3Dプリンター用データの作成方法は?データ作成後の手順やデータ作成時の注意点まで徹底解説」で詳しくご紹介していますので、こちらもチェックしてみてください。
3Dデータの準備が終わったら、3Dプリンターに材料などをセットします。
USBやWi-Fiを使って、作成した3Dデータ(スライスデータ)を3Dプリンターに入れると、造形スタートです。
造形工程
3Dプリンターは、基本的に全自動で造形を行います。そのため、造形中にすることは特にありません。
後工程
後工程は、3Dプリンターの造形方式によってさまざまですが、後工程の発生しない3Dプリンターは存在しません。
造形方式や材料に応じた方法で、付着した余分な材料を取り除いたり、サポート部の除去を行ったり、造形物の表面を研磨して滑らかにしたりといった後処理が一般的です。
造形方式によっては、ステージから造形物を剥離するところから後工程が始まるものも。
造形物に求める仕上がりによって、塗装やコーティングといった後加工を行う場合もあります。
3Dプリンターでの造形に必要なサポート部とは?
先ほどから、何度が登場している「サポート部」ですが、3Dプリンターで造形をするなら、サポート部については必ず理解しておく必要があります。
サポート部とは、簡単に言うと、3Dデータには存在しない、造形物が崩れたり倒れたりしないようにするための仮の支えです。
アルファベットのYの斜めに迫り出した部分や、HやTの宙に浮いた部分、また、材料の収縮によって変形しやすい部分などをサポート部で支えておくと、その部分の落下や破損、変形などを防ぐことができるのです。
このようにお伝えすると、サポート部はたくさんあった方が良いと考える方もいらっしゃると思いますが、サポート部は必要最低限にしましょう。
サポート部がたくさんあった方が、精度が高まる場合が多いのですが、サポート部は後工程で除去する必要があり、あまりに多すぎると後工程の手間が増えたり、きれいに除去するのが困難になったりするからです。またサポート部が多いと、その分材料費もかさんでしまいます。
先ほど、サポート部は、3Dプリンターの専用ソフトウェア(スライスソフト)で自動的に設定してくれることも多いとお伝えしましたが、3Dプリンターを活用する上では、手動で最適な設定ができるスキルを身につけられるとベストです。
こればっかりは経験が物を言うため、何度も造形を繰り返して、このデザインのパターンはこのくらいのサポート部が必要、この角度ならサポート部は不要、この位置のサポート部は仕上がりに影響するから移動といった判断を徐々にしていけるようになるしかありません。
造形方式によっては、造形物とサポート部を別の材料で造形することが可能です。サポート部専用の材料を使用すれば、洗浄するだけでサポート部をきれいに除去できるなど、後工程が楽になります。
一方、造形物とサポート部を同じ材料で造形しなければならない造形方式もあります。この場合は、必ず、一つ一つのサポート部を手作業で除去しなければなりません。なるべくサポート部を細くするなどして、後処理がしやすくなる工夫をするのがおすすめです。
このように、サポート部は3Dプリンターで造形する上で、欠かせない存在です。
3Dプリンターを選ぶ際には、各製品のサポート部の造形についてもしっかり確認しておくことをおすすめします。
3Dプリンターの7つの造形方式
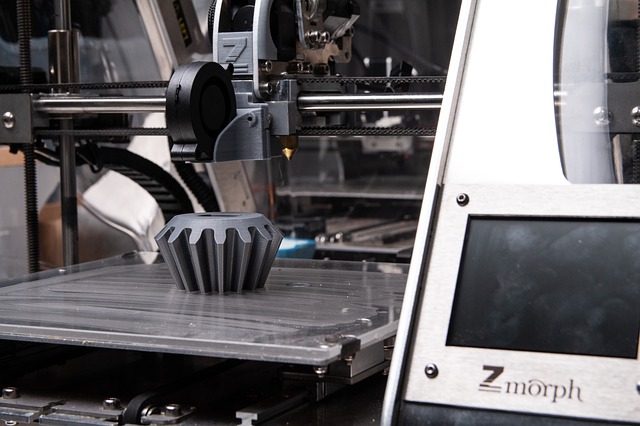
3Dプリンターの仕組みや基礎知識について解説をしたところで、ここから主な7つの造形方式についてご紹介していきます。
3Dプリンターの基本の造形の仕組みが頭に入っていれば、それぞれの造形プロセスや違いがよくわかるはずです。
材料押出方式/熱溶解積層方式(FDM方式)
3Dプリンターで、現在最も主流な造形方式が、材料押出方式/熱溶解積層方式です。
材料として使用するのは、フィラメントと呼ばれる熱可塑性樹脂を固めた紐状のもの。
ノズルから溶かしたフィラメントを押し出し、一筆書きの要領で一層一層積み上げていきます。
フィラメントは扱いやすく、また、純正品だけでなく、サードパーティ製のフィラメントもたくさん販売されており、材料の選択肢が豊富なのも魅力の一つ。
ノズルが2つ付いた製品であれば、造形物とサポート部を別の材料で造形することができます。
デメリットとしては、積層部分の凹凸が目立ちやすいことと、造形物の強度は比較的高いのですが、積層方向に対して垂直の力に弱いことが挙げられます。
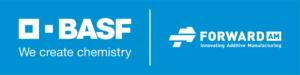
液槽光重合方式/光造形方式(SLA方式/DLP方式)
液槽光重合方式/光造形方式は、3Dプリンターの造形方式の中で最初に実用化された方式で、材料押出方式/熱溶解積層方式と同じく、現在主流の造形方式です。
紫外線で固まる光硬化性樹脂を満たしたプールの中にステージをセットし、UVライトやレーザーを照射することで一層分ずつ硬化して積層していきます。
上からUVライトやレーザーを照射して、ステージの上に造形物ができるタイプと、プールの下から照射して、ステージの下に宙吊りになるように造形物ができるタイプがありますが、後者の製品の方が一般的です。
SLA方式とDLP方式では、一度に照射できる面積が違い、SLA方式は点で、DLP方式は面で照射をするため、DLP方式の方が造形スピードが速いです。
液槽光重合方式/光造形方式のメリットは、高精度で滑らかな造形物を作れること。また透明度の高い造形物や大型の造形物にも対応しています。
一方、洗浄が必要であったり、造形物とサポート部が同じ材料のため、手作業で除去する必要があったりと後工程に手間がかかります。
材料噴射方式/マテリアルジェッティング(インクジェット方式)
材料噴射方式/マテリアルジェッティングは、紫外線で固まる光硬化性樹脂をインクヘッドから噴射し、UVライトを照射して硬化というプロセスを繰り返して積層していく造形方式です。
光硬化性樹脂を使用して紫外線で硬化するのは、液槽光重合方式/光造形方式と同じですが、液槽光重合方式/光造形方式は、液体の樹脂を満たしたプールにステージを浸ける、材料噴射方式/マテリアルジェッティングは、ステージに材料を噴射するという、材料の供給方法に大きな違いがあります。
高精細で滑らかな造形物を作れるほか、色や材料を混ぜることができるため、フルカラーでの着色や材料を混合した造形物の製作が可能です。
また造形物とサポート部の材料を別のものにできるため、除去の手間は少ないですが、造形する過程で空洞になる部分全てにサポート剤が必要なため、ややコストがかさみます。
結合剤噴射方式/バインダージェッティング(インクジェット方式)
結合剤噴射方式/バインダージェッティングは、ステージに粉末材料を敷き詰めて、インクヘッドから接着剤(バインダー)を噴射するというプロセスを繰り返して積層していく造形方式です。
材料噴射方式/マテリアルジェッティングと似た造形方式ですが、使用する材料が粉末であることと、インクヘッドから噴射するのが接着剤(バインダー)であるという点が大きく異なります。
造形物は粉末を接着しただけの非常に脆い状態のため、必要な強度に応じて、改めて接着剤を塗布したり、接着剤に付け込んだりと言った含浸処理を行います。尚、敷き詰めた粉末材料が支えになるため、サポート部を造形する必要がありません。
結合剤噴射方式/バインダージェッティングでは、粉末であればどんな材料でも使用できるため、石膏や砂だけでなく、金属粉末を使用できたり、食品を製造できる「3Dフードプリンター」の開発も進められています。また接着剤(バインダー)に着色料を混ぜることで、フルカラープリントも可能です。
粉末床溶融結合方式/粉末焼結方式(SLS方式)
粉末床溶融結合方式/粉末焼結方式は、結合剤噴射方式/バインダージェッティングのバインダーが、レーザー光線や電子ビームに置き換わったものと考えるとわかりやすいと思います。
ステージに粉末材料を敷き詰め、レーザー光線や電子ビームを照射して焼結するというプロセスを繰り返して、積層していきます。
粉末材料を敷き詰めるため、基本的にサポート部は不要なのですが、金属粉末で造形する場合はサポート部を造形する必要があり、その除去作業はなかなか大変です。
またデメリットとして、健康被害や事故を防ぐために必要な設備が多く、導入が大掛かりになってコストもかさむということが挙げられます。
シート積層方式
シート積層方式は、薄いシート状の材料をスライスの輪郭に沿ってカットし、接着しながら積み重ねていく造形方式です。
材料は紙が主流ですが、シート状の金属や樹脂も使用できます。
材料のシートが積み重ねられた中から造形物を取り出す必要があるため、後工程で不要部分の除去作業が必要になります。
指向性エネルギー堆積方式/レーザーデポジション
指向性エネルギー堆積方式/レーザーデポジションは、金属3Dプリンターに使用される造形方式です。
金属粉末の噴射とレーザービームの照射を同時に行い、溶けた金属を積層、凝固させて造形していきます。
一から造形するだけでなく、摩耗部分を肉盛り修復する加工(レーザークラッディング)も可能です。
造形できる形状に制限があり、サポート部が必要になるようなデザインの造形には向きません。また造形精度もそれほど高くないため、使用用途が限られます。
3Dプリンター選ぶ際は導入目的を明確に!
最後に、3Dプリンターの基礎知識として、3Dプリンターを選ぶ際の最重要ポイントを一つお伝えしたいと思います。それは、3Dプリンターを導入する目的を明確にすることです。
ここまでご紹介してきたように、3Dプリンターには主に7つの造形方式があり、材料や材料の供給方法、結合方法、メリットデメリットなどに違いがあります。
実際に3Dプリンターを選ぶ際は、7つの造形方式の中から1つに絞った上で、さらに、同じ造形方式で特徴の異なる複数の製品を比較検討しなければなりません。
導入目的が明確であればあるほど、製品が選びやすくなり、またミスマッチな製品を選ぶ可能性も低くなるため、あれを作りたい、あれを実現したいといった明確な導入目的を持っておいた方が良いのです。
導入する製品に迷った場合は、3Dプリンターに詳しいプロの力を借りるのも一つの手です。 日本3Dプリンター株式会社には、3Dプリンティングや3Dスキャンニングの専門知識を持ったスタッフがおりますので、ぜひ、お気軽