3Dプリンターの光造形方式とは? 造形プロセスやメリット・デメリットなどについて解説!
2021.04.26 更新日:2024.03.05
- 3Dプリンター
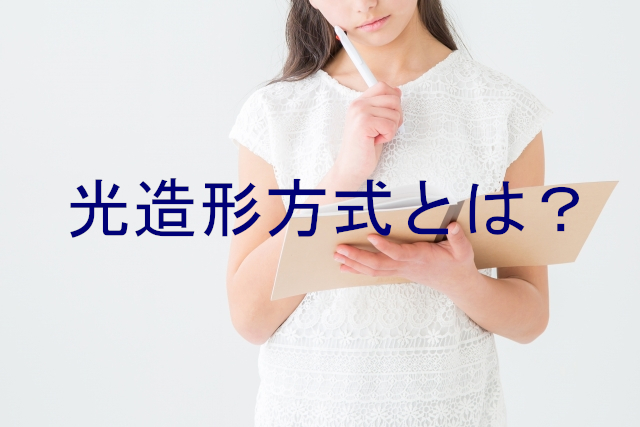
一口に3Dプリンターと言ってもさまざまな種類があり、造形方式によって、使用できる材料や特徴が異なります。
目的に対して最適な3Dプリンターを選ぶには、まずそれぞれの造形方式の特徴を知っておくことが大切です。
この記事では、3Dプリンターとして最初に実用化された、光造形方式について詳しくご紹介していきます。
光造形方式とは?
光造形方式は、3Dプリンターの主たる7つの造形方式のうちの1つで、最も歴史のある造形方式です。
液体の光硬化性樹脂(レジン)に、UVライトやレーザーを照射することで1層ずつ硬化、積層していき、造形物を作り上げます。
光造形方式の歴史
世界で最初に、光造形方式の3Dプリンターと同様の技術である「光造形法」を生み出したのは、なんと日本人。名古屋市工業研究所の研究者であった小玉秀男氏が、1980年に「立体図形作成装置」として特許出願しています。
そして、世界で初めて光造形法を実用化させたのが、世界の二大3Dプリンターメーカーの一つ『3Dsystems』の創業者であるチャック・ハル氏です。
チャック・ハル氏は、1986年に光造形方式のうちの一つであるSLA方式の米国特許を取得。同じく1986年に『3Dsystems』を設立し、翌年1987年には、最初の光造形装置「SLA-1」を販売開始します。
2006年に『3Dsystems』のSLA方式の特許が失効したため、現在は、さまざまなメーカーが光造形方式の3Dプリンターを開発・販売しています。
関連記事:【プロの解説!】3Dプリンターが進化した歴史背景とは?
光造形方式の造形プロセス
光造形方式の3Dプリンターの中にもいくつかタイプがあり、光やレーザーを上から照射するものと下から照射するもの、また光やレーザーを点で照射するSLA方式と、面で照射するDLP方式があります。
ここでは、現在、光造形方式の3Dプリンターで主流な、光やレーザーを下から照射するタイプを例に、造形プロセスを説明していきます。
1.光硬化性樹脂を満たしたプールの中に、造形物が作られるテーブルを浸けます。
2.プールの底面から、光やレーザーが照射され、1層目の硬化を行います。
3.1層目の硬化が完了したらテーブルが持ち上がり、プールの底面から剥離させると共に、余分な光硬化性樹脂を落とします。
4.先ほどよりも1層分高い位置までテーブルが下がったら、再びプールの底面から、光やレーザーが照射され、2層目の硬化を行います。
このプロセスを繰り返すことによって、造形物が作り上げられていくのです。
光やレーザーを下から照射するタイプの3Dプリンターの場合、プロセス3のプールの底面から剥離させる工程が、非常に重要です。
無理に剥離させようとして造形物が破損してしまうことがあるため、このタイプの3Dプリンターを選ぶ際には、造形物をきれいに剥離させられるかどうかをチェックしておくことをおすすめします。
製品によっては、剥離しやすくするために、プールを左右に揺らすなどといった機能が備わっているものもあります。
光やレーザーを上から照射するタイプの場合は、プールの底面から剥離させるプロセスが無くなりますが、その代わりに、次の層を造形する用の光硬化性樹脂を、テーブルの上に満遍なく行き渡らせるプロセスや時間が必要になります。
SLA方式とDLP方式の違いは、主に、造形スピードです。面で照射できる分、DLP方式の方が早く造形物を完成させることができます。
造形精度については、一般的に、SLA方式の方がやや優れていると言われています。
関連コラム:3Dプリンターの造形の仕組みと知っておきたい基礎知識
光造形方式の後処理
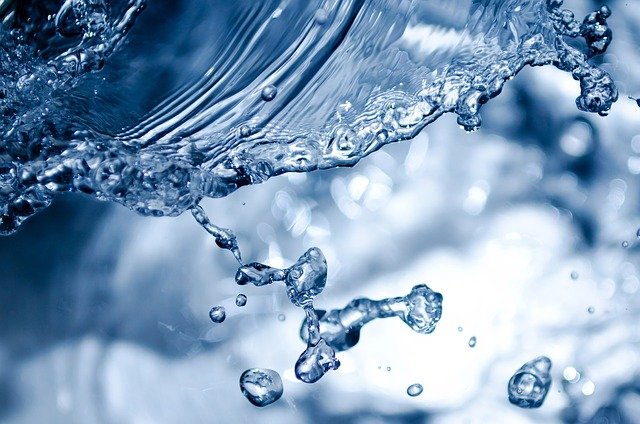
どの造形方式の3Dプリンターでも、ある程度の後処理が必要になりますが、光造形方式の場合は、洗浄と、必要に応じて二次硬化やサポート部の除去、また研磨が必要になります。
まず造形が終了したら、エタノールなどを使用して洗浄し、造形物に付着した未硬化の光硬化性樹脂を除去します。
表面だけでなく、細かい隙間などに入り込んだ液体樹脂もしっかり取り除く必要があります。
造形物が溶けてしまう可能性があるため、長時間洗浄液に浸けすぎないように注意しましょう。
洗浄が終わったら、必要に応じて二次硬化を行います。
使用する光硬化性樹脂や3Dプリンターの性能などによっては、造形時の光やレーザーの照射だけでは完全に硬化されておらず、半硬化の状態になっていることがあるからです。
半硬化の状態の造形物は、本来の強度などを実現できておらず、そのまま使用すると、変形や破損の恐れがあります。
特に高性能な樹脂を使用している場合は、しっかりと二次硬化を行いましょう。
造形に際して、サポート部が一緒に造形されている場合は、この段階でサポート部の除去を行います。
光造形方式の場合、造形物とサポート部が同じ材料のため、サポート部の除去にはやや手間がかかります。
サポート部が多い方が、造形物の精度は高くなりますが、多すぎるとサポート部の除去作業が困難になるため、必要最小限にとどめておくのがポイントです。またサポート部をニッパーなどで切断できるくらい細くしておくと、除去作業が楽になります。
サポート部を自動で設定してくれる3Dプリンターもありますが、経験を重ねて、必要に応じて作成者が調整できるようになるとベストです。
サポート部の除去が完了したら、造形物の表面を研磨して見た目を美しく仕上げていきます。
光造形方式は熱溶解積層方式(FDM方式)と比べて積層面が目立ちにくく、比較的この仕上げ作業が楽に済みます。
しかし、サポート部が多かったり、洗浄をしっかりせずに、二次硬化をしてしまったりすると研磨が大変になるため、サポート部は必要最小限にとどめると共に、二次硬化の前にしっかりと洗浄を行うようにしましょう。
光造形方式で使用できる主な材料
光造形方式で使用できる材料は、エポキシ系樹脂とアクリル系樹脂の大きく2つに分けられます。
エポキシ系樹脂で最も一般的な材料は、ABSライク樹脂とPPライク樹脂です。
ABSライク樹脂は、ABS樹脂同様強度があり、耐衝撃性や耐熱性などに優れていますが、ABS樹脂よりもやや強度が劣るため、そのまま代替品として使用することはできません。
PPライク樹脂は、PP(ポリプロピレン)樹脂の耐衝撃性や耐熱性などを再現しています。
アクリル系樹脂にはさまざまなタイプのものがあり、中には、透明度の高い樹脂も。この透明度の高い材料を使って、透明度の高い造形物を作ることができるのが、光造形方式の代表的な特徴の一つです。
造形直後は透明度の低い半透明の状態ですが、研磨やコーティングといった後工程を経ると、高い透明度を実現できます。
そのほか光造形方式では、耐久性や耐熱性に優れた樹脂、弾性のあるゴムやエラストマーを再現したようなゴムライク、ロストワックス精密鋳造のワックスの代わりになる樹脂など、さまざまな材料が使用可能です。
メーカーによって取り扱っている樹脂が異なり、同じタイプの樹脂でも細かい性能に違いがあるため、製品選びの際には、希望する材料がメーカー純正品として販売されているかどうかもチェックすることをおすすめします。
関連記事:3Dプリンターで使用できる素材にはどんなものがある?
光造形方式の特徴・メリット
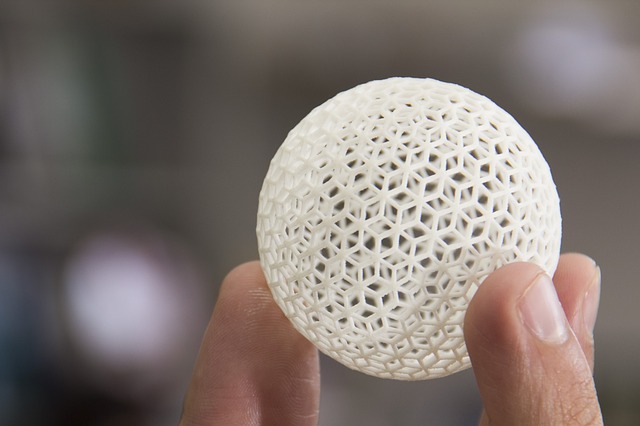
ここからは、光造形方式の3Dプリンターの特徴やメリットをご紹介していきます。
造形スピードが速く生産力が高い
光造形方式は、比較的造形スピードが速い造形方式です。
特にDLP方式では、1個造形する場合と複数造形する場合で造形時間が変わらないため、3Dプリンターの造形方式の中でも、生産能力の高い方式であると言えます。
DLP方式は、1個造形する場合と造形時間が変わらず、SLA方式でも、個数に比例するのではなく、1.1~1.2倍程度の造形時間で済みます。
そのため、3Dプリンターの造形方式の中でも、生産能力の高い方式であると言えます。
造形精度が高い
光造形方式では、光硬化性樹脂を使用するため、熱溶解積層方式(FDM方式)などのように材料が高温にならず、熱収縮を起こしにくいです。そのため、寸法などの精度が高い造形物を造形することができます。
滑らかな仕上がり
積層痕が目立ちにくく、表面が滑らかな仕上がりになるのも光造形方式の特徴の一つです。
積層していく際に、硬化する層と一つ前に硬化された層がしっかりと結合するため、層と層の境目が目立ちにくいのです。同様の理由から、面による耐久性の差もほとんどありません。
また塗装などの後加工がしやすいというのも、仕上がり面でのメリットの1つと言えるでしょう。
そのため、フィギュアや模型をはじめとした、見た目を重視する最終製品の造形にも光造形方式は向いています。
透明度の高い造形物を製作可能
光造形方式最大の特徴が、アクリル系樹脂を使用して、透明度の高い造形物を作れることです。
研磨やコーティングといった後工程は必要ですが、高い透明度を実現することができ、これは、他の造形方式には真似できません。
実際、車のライトやLEDライトなどの試作品の作成に使用されています。
大型で高精度な造形物も製作できる
光造形方式の3Dプリンターには、大型のものも存在するため、大型で高精度な造形物も作ることが可能です。
ただし、光やレーザーを下から照射するタイプの場合、大型の造形物が造形途中で落下してしまう恐れもあるため、注意して造形する必要があります。
光造形方式のデメリット
メリットの多い光造形方式ですが、いくつかデメリットも存在します。
造形物が直射日光に弱い
光造形方式では、紫外線で硬化する光硬化性樹脂を使用しているため、長時間日光に晒されると、変形したり破損してしまったりする恐れがあります。
そのため、長時間外で使用するものの造形には不向きです。
材料の保管に手間やコストがかかる
光硬化性樹脂は、環境光によっても硬化したり、変質してしまったりするため、基本的には冷暗所で保管する必要があります。
材料の量や種類が多いと、保管のためのコストも多少かかってくるでしょう。
後処理の工程がやや手間
先ほど後処理についてご説明しましたが、3Dプリンターの造形方式の中では、比較的後処理に手間がかかる方に分類されます。
洗浄をしっかり行わなければならず、また自治体によっては、洗浄後の液体をそのまま下水に流せず、別途処理が必要になる可能性も。
さらに造形物とサポート部の素材が同じため、専用のサポート材を使用できる造形方式と比べると、サポート部の除去にも手間がかかります。
光造形方式の3Dプリンターが向いているシーン
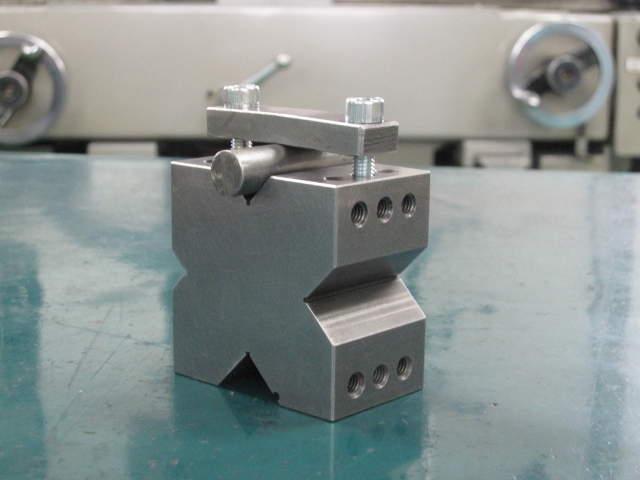
使用できる材料やメリット・デメリットなどを考慮すると、光造形方式の3Dプリンターは以下のようなシーンでの活用が向いています。
試作品の作成やラピッドプロトタイピング
3Dプリンターの主な導入目的の1つである試作品の作成に、光造形方式の3Dプリンターはぴったりです。
造形した試作品は、形状の確認はもちろん、パーツとパーツの嵌合の確認や機能性試験にも活用できます。
もちろん、ラピッドプロトタイピングでも大活躍。
造形時間が早く、造形物のサイズによっては、複数のパターンの試作品を同時に短時間で造形することも可能です。
治具・工具の作成
治具や工具は、製品ごとに専用のものを用意しなければならないことも少なくありません。3Dプリンターがあれば、3Dデータを用意したり、必要に応じて修正したりするだけで、作業で必要な治具や工具を簡単に造形することが可能です。
光造形方式は、造形精度が高く、耐久性や耐熱性に優れた樹脂を使用できるため、治具や工具の造形にも向いています。
金型の作成
上記と同様の理由から、光造形方式の3Dプリンターで金型を作成することも可能です。金型を作成する場合は、特に二次硬化をしっかりと行いましょう。
未硬化の部分が残っていると、流し込む樹脂と金型が化学反応を起こし、上手く形成できなくなってしまいます。
ロストワックス精密鋳造のワックスモデルの作成
ロストワックス精密鋳造とは、アクセサリーや、歯科治療に使用される金属部品などを作る際に使用されている鋳造方法の一種です。
ワックスで作りたいパーツの原型を作り、その周囲を鋳砂やセラミックなどで覆い固めて加熱します。すると中のワックスモデルが溶けて除去され、鋳型ができ上がるのです。
このワックスモデルを、光造形方式の3Dプリンターで造形することができます。
ワックスの代わりとなる樹脂を使用し、光造形方式の3Dプリンターで造形をすることで、これまで使用されてきたワックスモデルの型では作れなかった、デザイン性の高いワックスモデルを造形することができたり、複数のワックスモデルを一度に多量に造形して、作業工程をギュッと圧縮したりすることができます。
フィギュア・模型・最終製品の造形
精度が高く、見た目の滑らかな造形物を作り出せるというメリットを生かして、見た目重視のアイテムの造形にも活用できます。フィギュアや模型はその典型例です。
またもちろん、最終製品の造形にも活用できます。
ただし、3Dプリンター共通の特徴として、大量生産には向かないこと、そして、光造形方式で作った造形物は、屋外での長時間の使用には向かないことから、ある程度、造形できる製品は限られてしまいます。
オーダーメイドや受注生産のアイテム、室内利用が主なアイテムであれば、光造形方式の3Dプリンターでも十分造形可能です。
関連製品:DLP方式光造形3DプリンターRaise3D「DF2」